Eqrader turns MSP Onions into a showcase for automatic sorting
In collaboration with Link Magazine & Wilma Schreiber, September 2021
Zeeland is currently the epicenter for onion processing in the Netherlands and the rest of the world. And MSP Onions in Nieuwdorp has the world’s largest automated onion processing line, realized by Eqraft in Emmeloord, with an integrated optical sorter named Eqrader. The line is 40 meters long, with 16 outputs for exactly the right onions in terms of size, color, shape, weight and internal and external quality.
Eqraft focuses on the agrobulk market for onions and potatoes, with an occasional excursion to the legume market (granules, nuts, peas, seeds, etc.). The company is unique in that it does everything in-house – from engineering to constructing and assembling machines, but also electrical work and software – so that it can offer its customers a total solution. Eqraft’s markets are located around the world wherever labor is scarce or expensive, such as the US West Coast, New Zealand and Australia. ‘Wages are rising there, and that makes manual sorting more expensive and increases the need for automation. We used to be too expensive but now we’re much more affordable,’ says Rutger Keurhorst, Commercial Manager and also responsible for sales engineering.

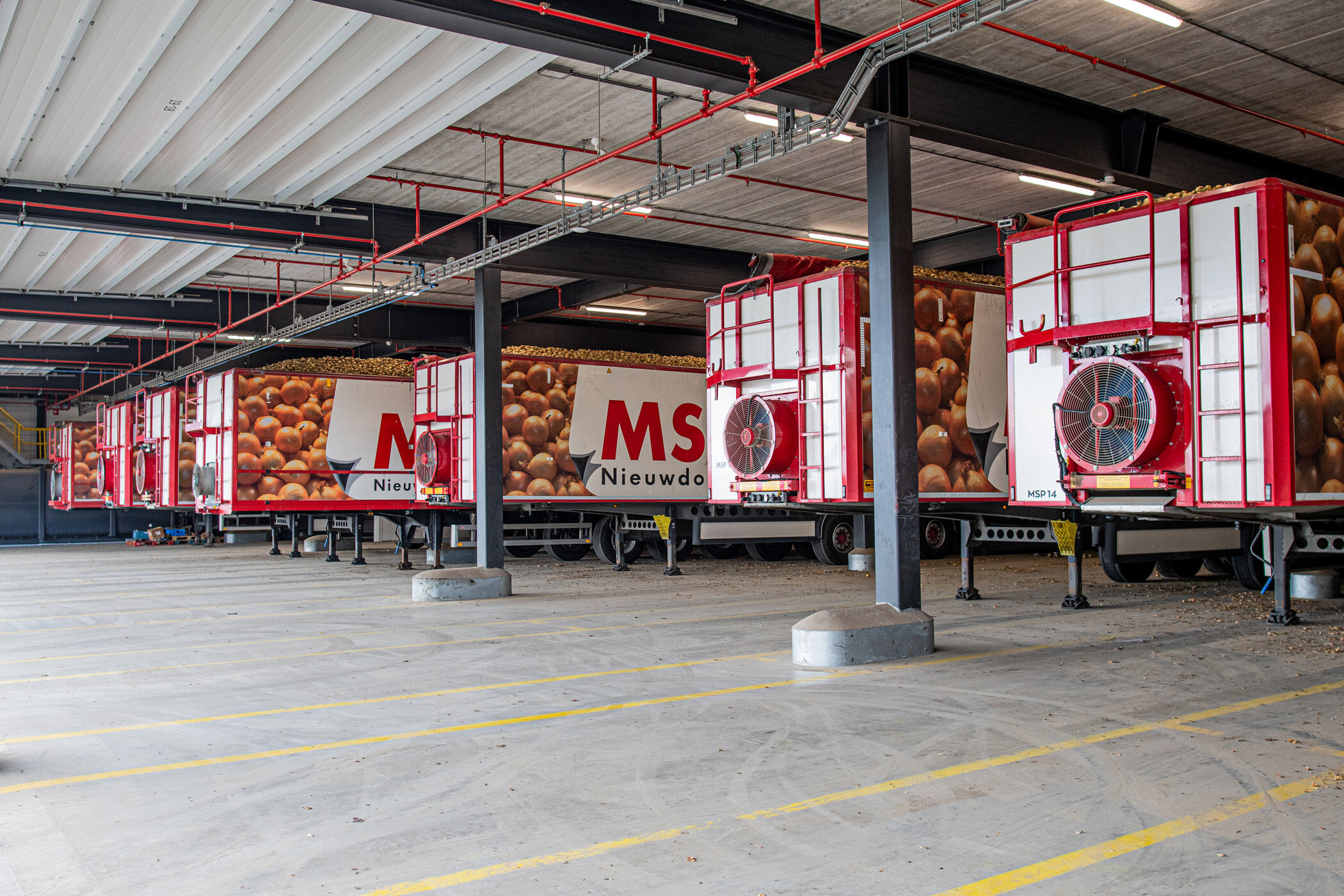
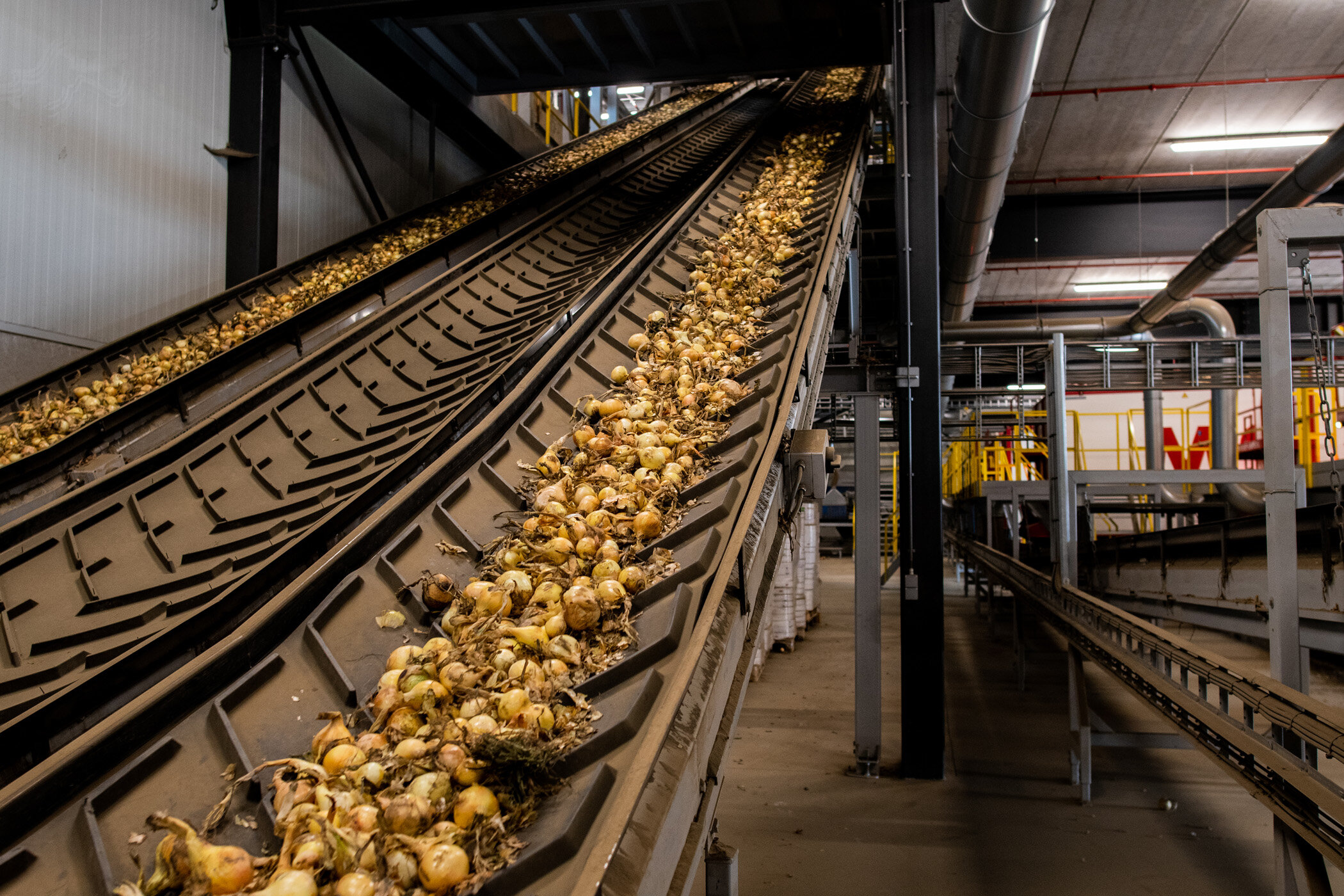
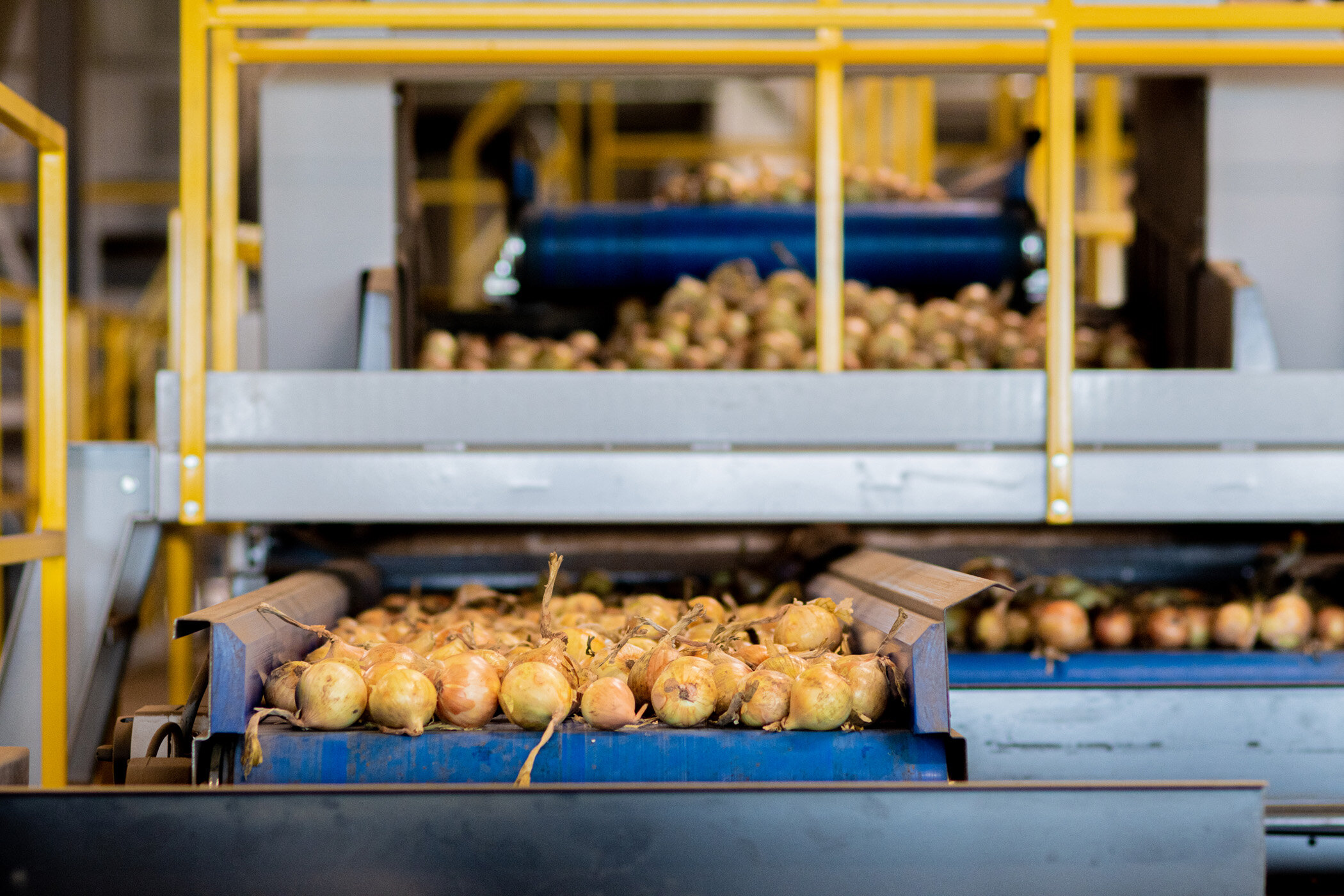
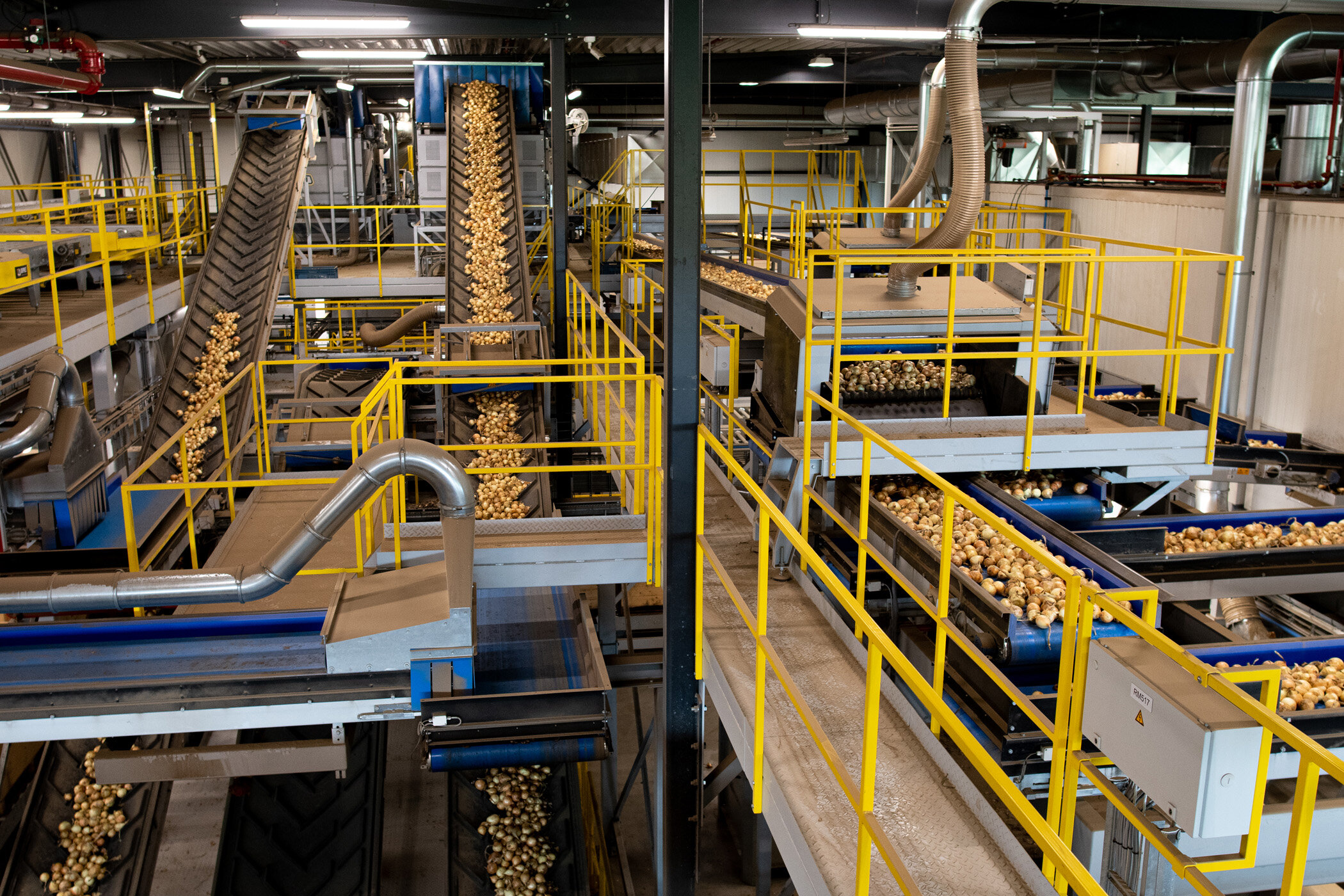
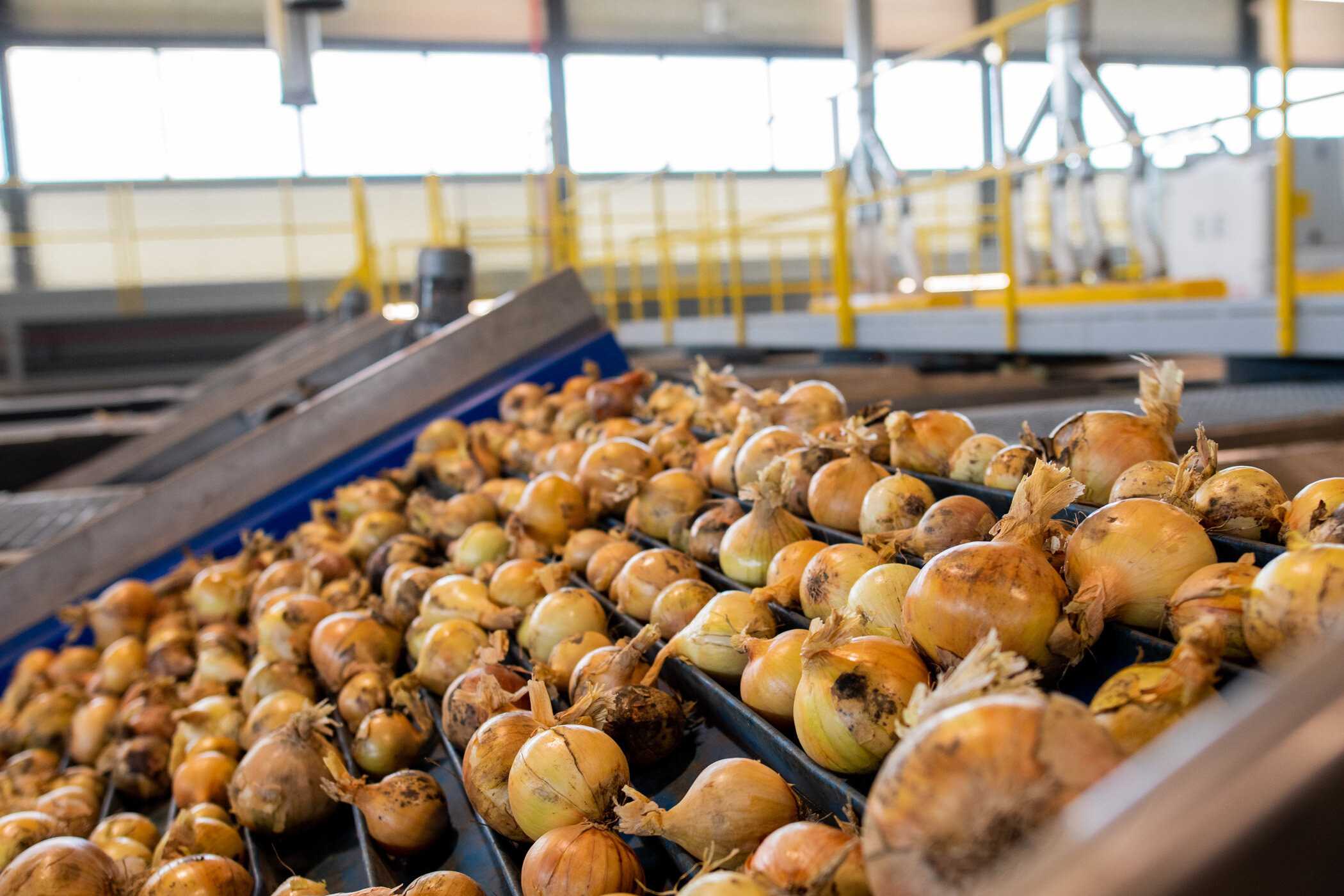
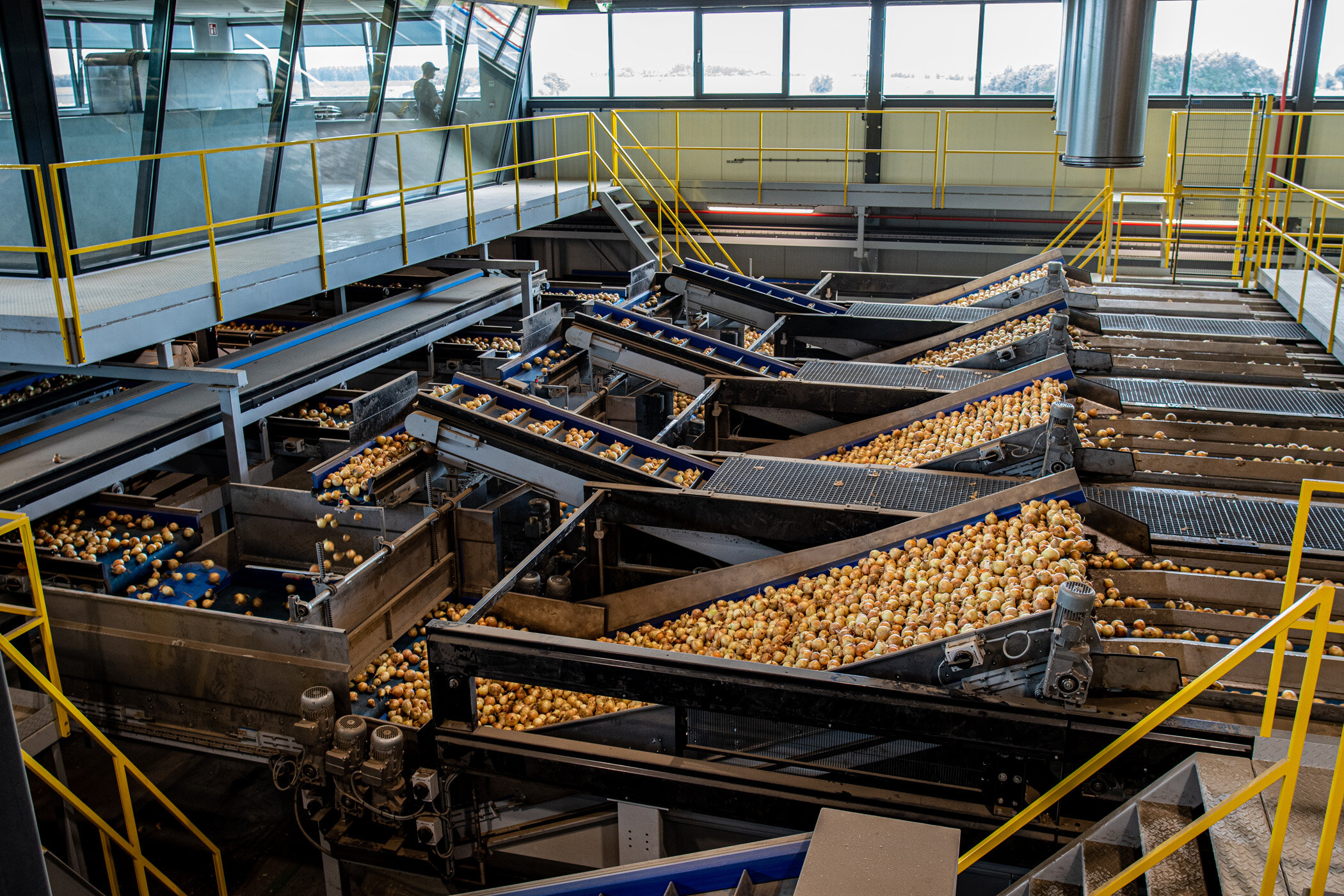
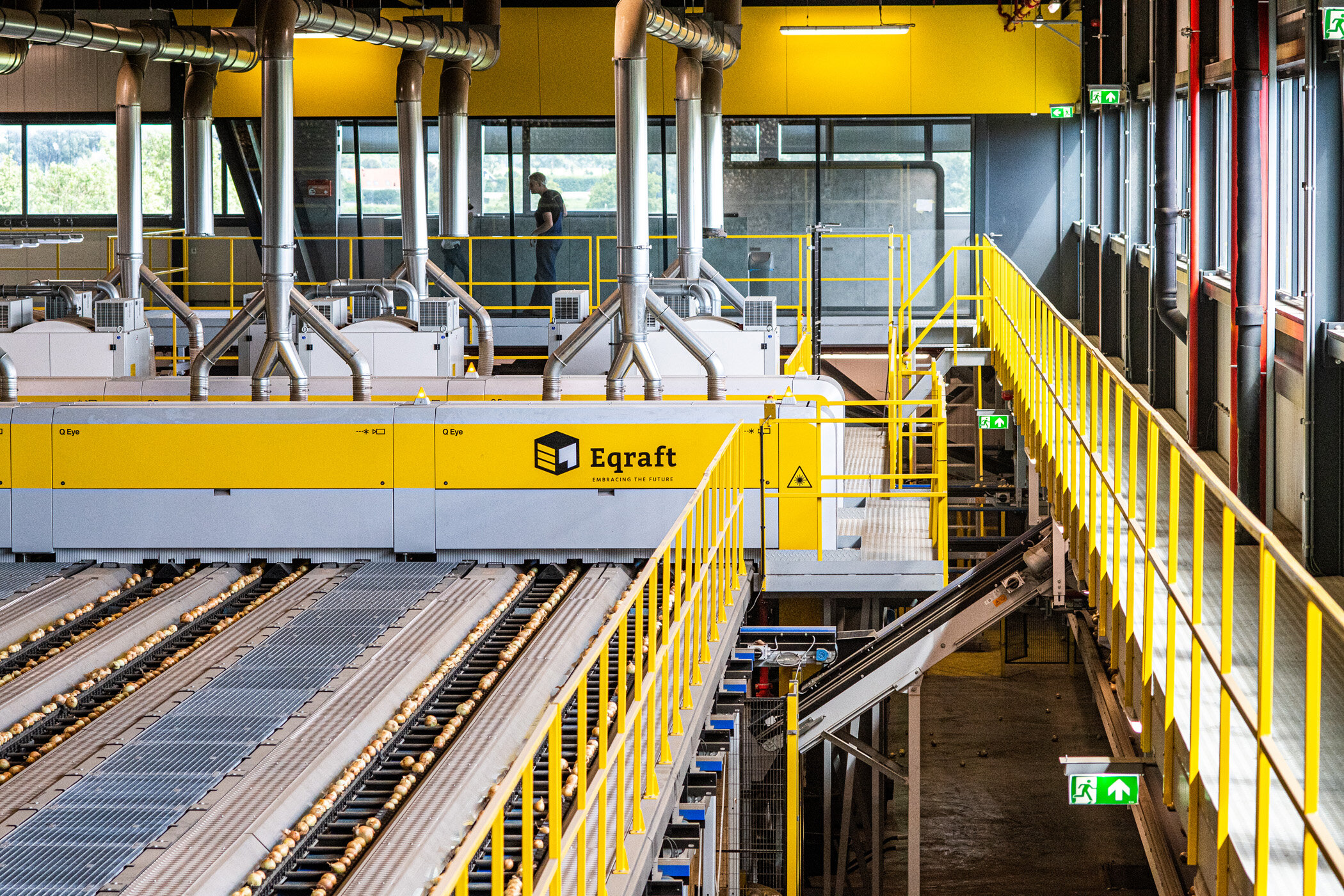
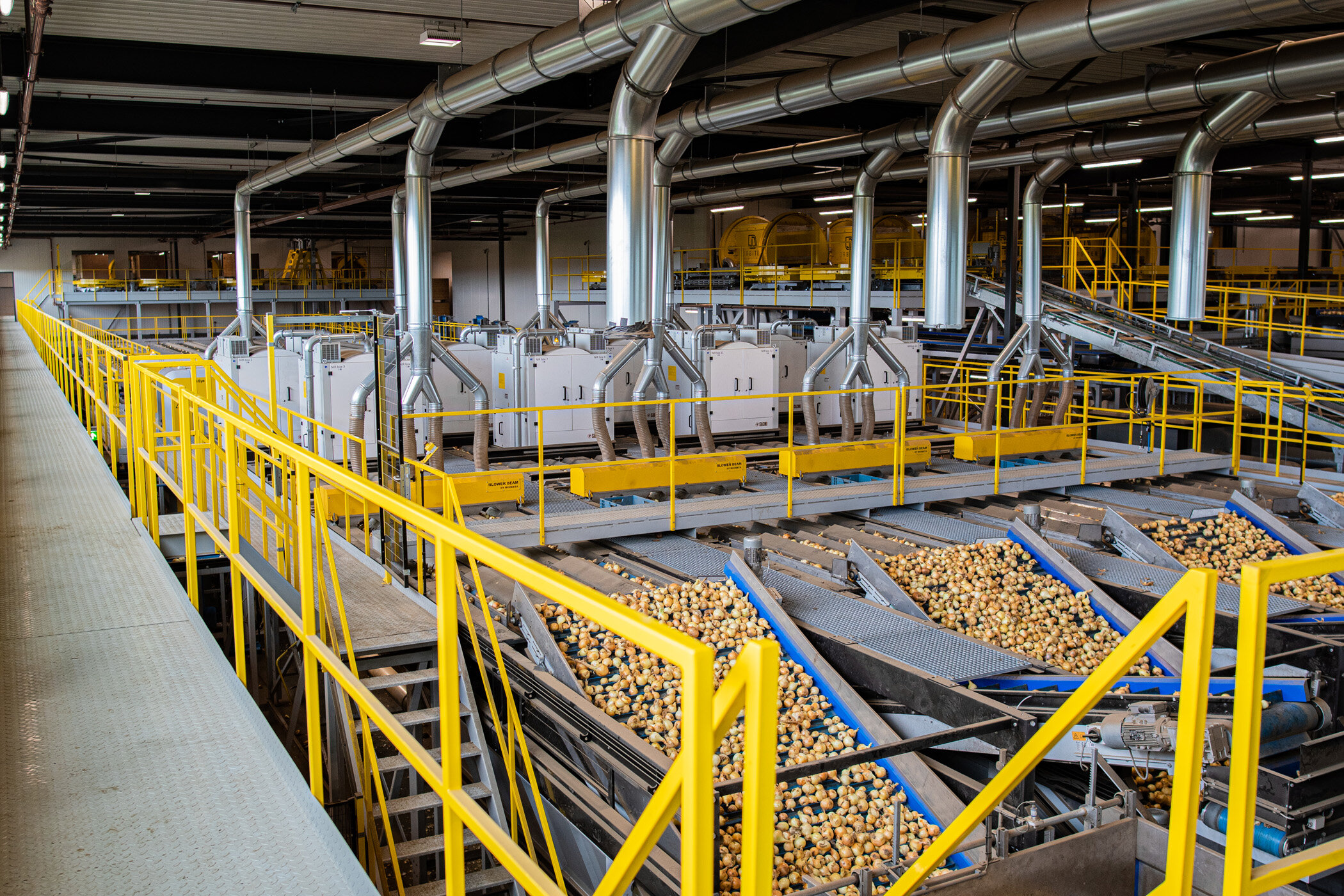
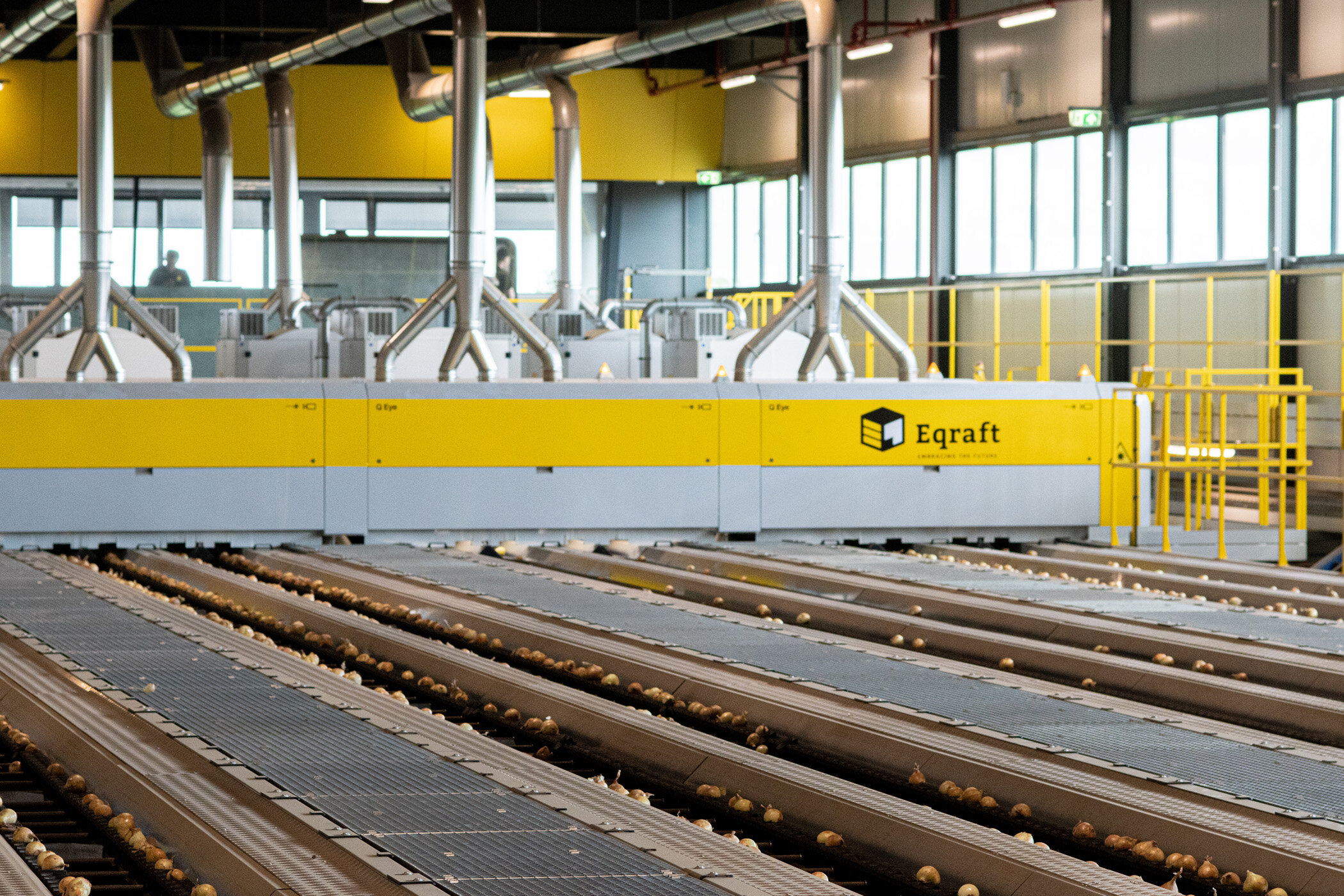
Extra dimensions
The Eqrader gives customers the option of sorting their onions on item level, such as by internal quality. ‘If a product has been on a ship from the Netherlands to Indonesia for six weeks, you want to know up front that it will pass inspection on arrival,’ says Keurhorst. ‘Added to that, the quality of manual sorting isn’t as good as it used to be, especially as volumes and operating hours increase. While quality, warranty and traceability are becoming more and more important for customers.’ So an optical sorter is then the most logical solution. ‘We’re now at the level where the computers, software and analysis technologies are so smart that you can guarantee better quality than when products are sorted by humans.’
“We’re now at the level where the computers, software and analysis technologies are so smart that you can guarantee better quality than when products are sorted by humans.”
Tailored to sales opportunities
This gives customers a completely different spectrum of sorting options. For example, an optical sorter can select on the basis of external quality, size and shape, color, internal quality and weight. ‘You can extract a perfectly round onion in a certain millimeter class from a batch of 500 tons to guarantee that extremely high-quality bar packaging in the supermarket. Or onions with some weathering on the outside but otherwise good, which are suitable for distant destinations because the outer skin falls off anyway during transport,’ says Keurhorst. The selections can then be linked to an output. The shortest Eqrader has six outputs, but the number is basically endless and is just a matter of making the machine longer. To determine the quality, the machine uses a self-learning system that combines data. ‘There are six cameras per position for the greatest possible overlap: photograph one side of the onion, tilt it out, photograph the other side,’ says Keurhorst. ‘Thanks to infra-red technology, the Eqrader also detects rot inside the onion, starting from 2 percent of the bulb volume. Something that the human eye cannot see but that’s crucial for quality.’
“You can change the complete production line with just one mouse click.”
Simpler flow
This trend-setting evolution of knowledge and development attracted the attention of MSP Onions in Nieuwdorp in the Dutch province of Zeeland. Together with Eqraft, they built the Factory of the Future there. This is a completely new, fully automated factory that takes the vulnerability of onions into account. It is also home to the biggest Eqrader: 40 meters long with sixteen outputs. Just five people can run the factory at full capacity. The only forklifts that are there are for loading the trucks. ‘We’ve analyzed the entire logistics flow,’ says Keurhorst. ‘We ultimately opted for a three-layer factory with a simpler flow. That means that the onions require a shorter route. After receipt, they go up once, and then only down – gentle product handling – until they arrive on the pallet. Forty years of experience in sorting and packing onions, combined with new technologies, has led to flexibility on the line and short changeover times thanks to live data about the product. You can change the complete production line with just one mouse click.’
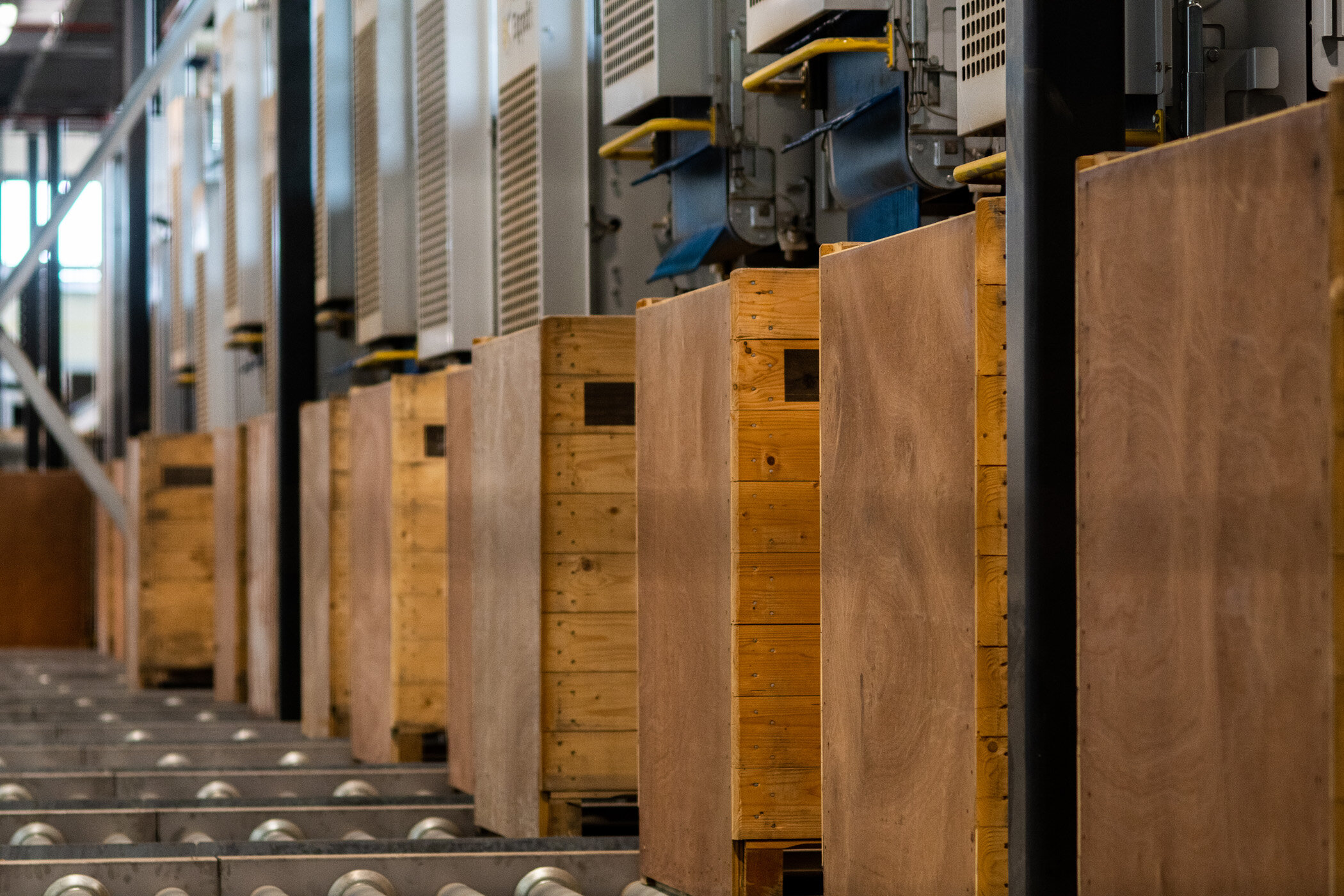
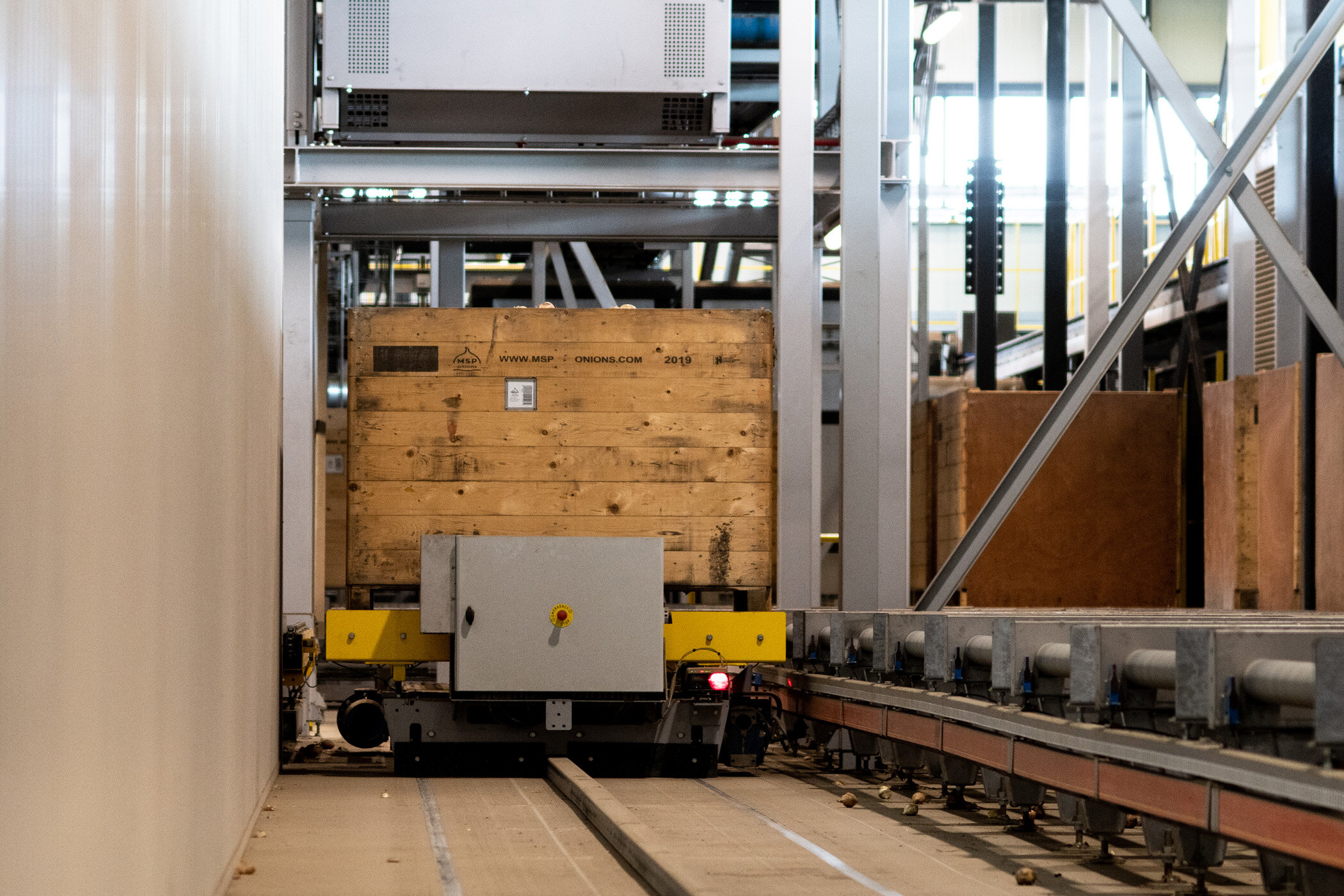
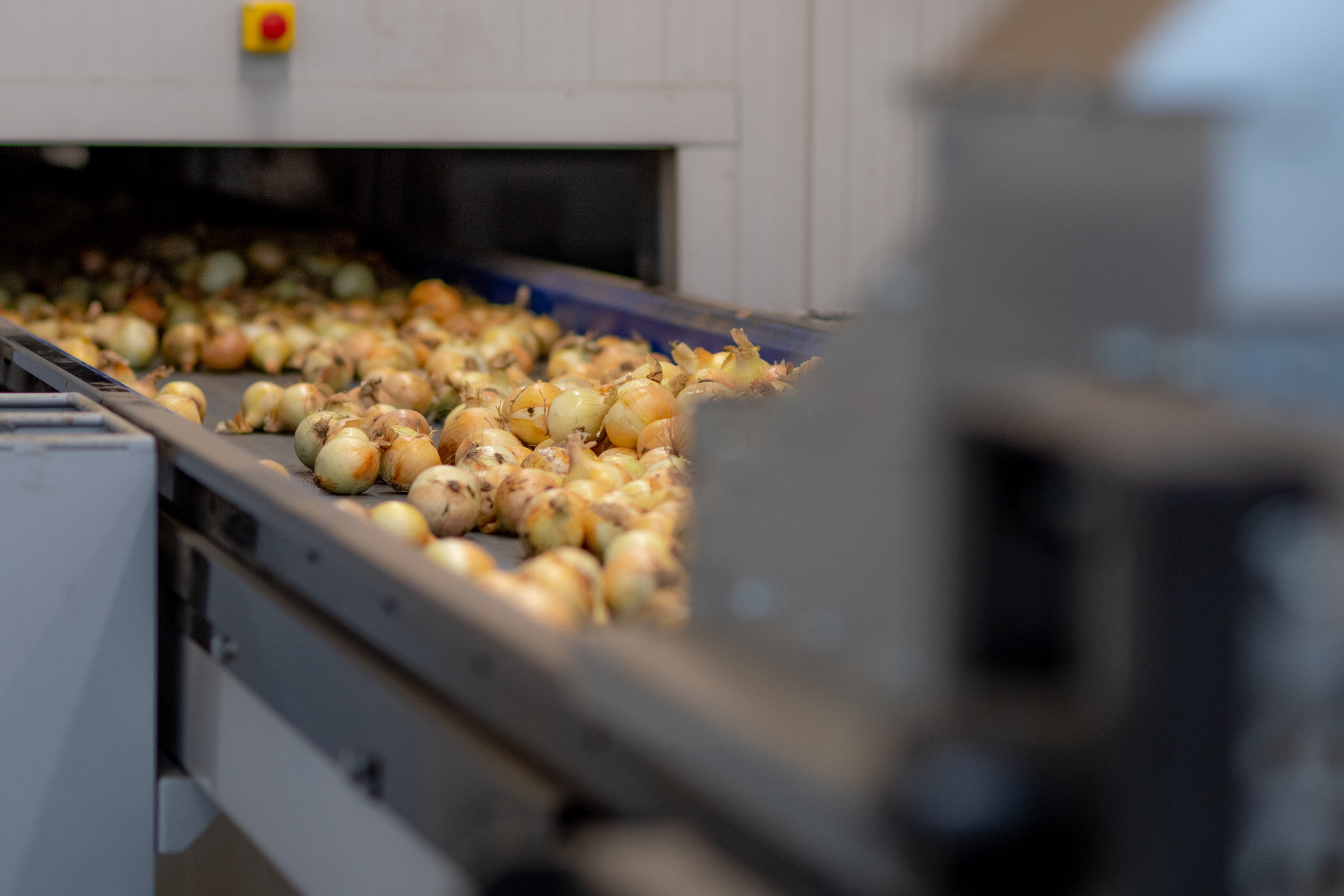

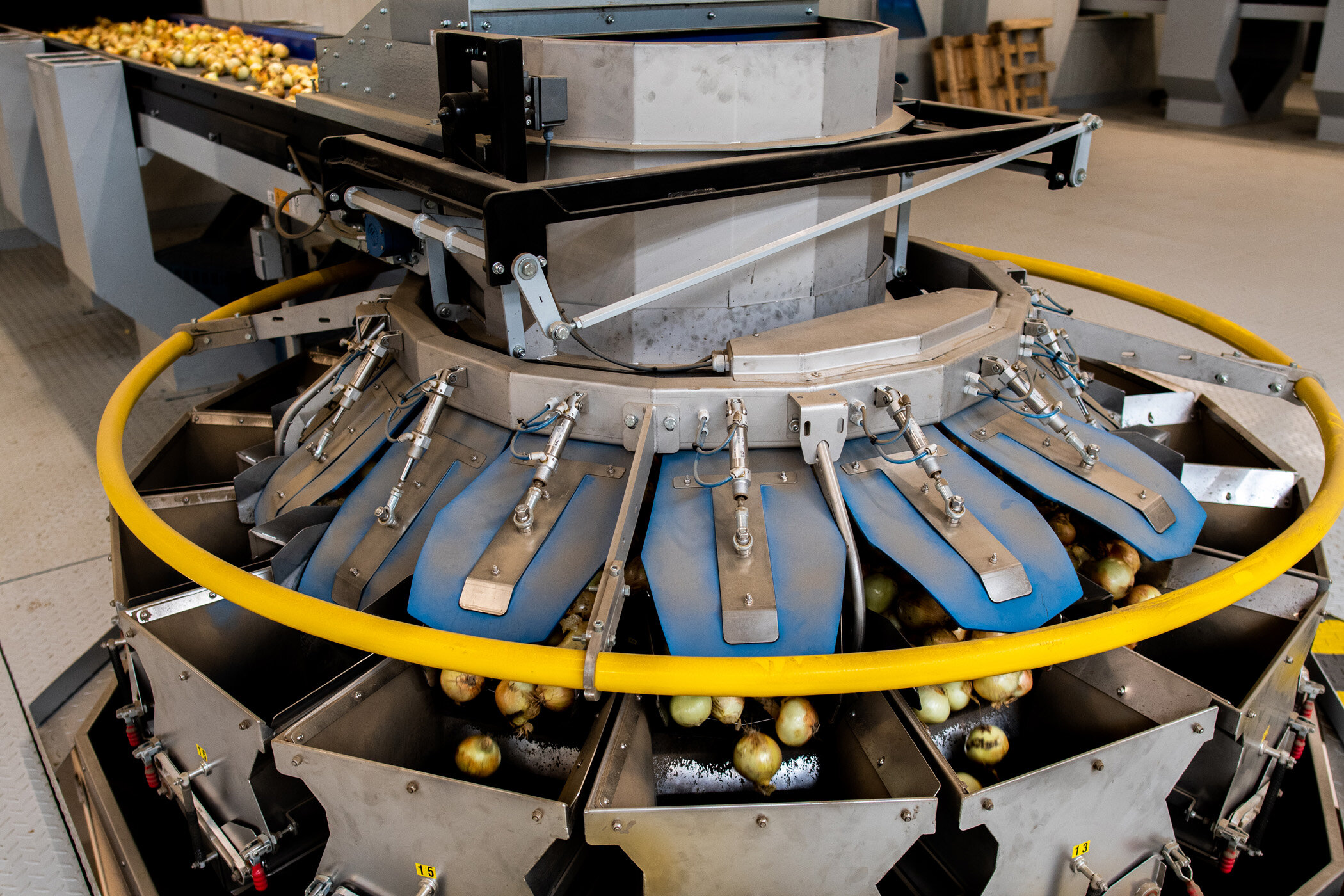
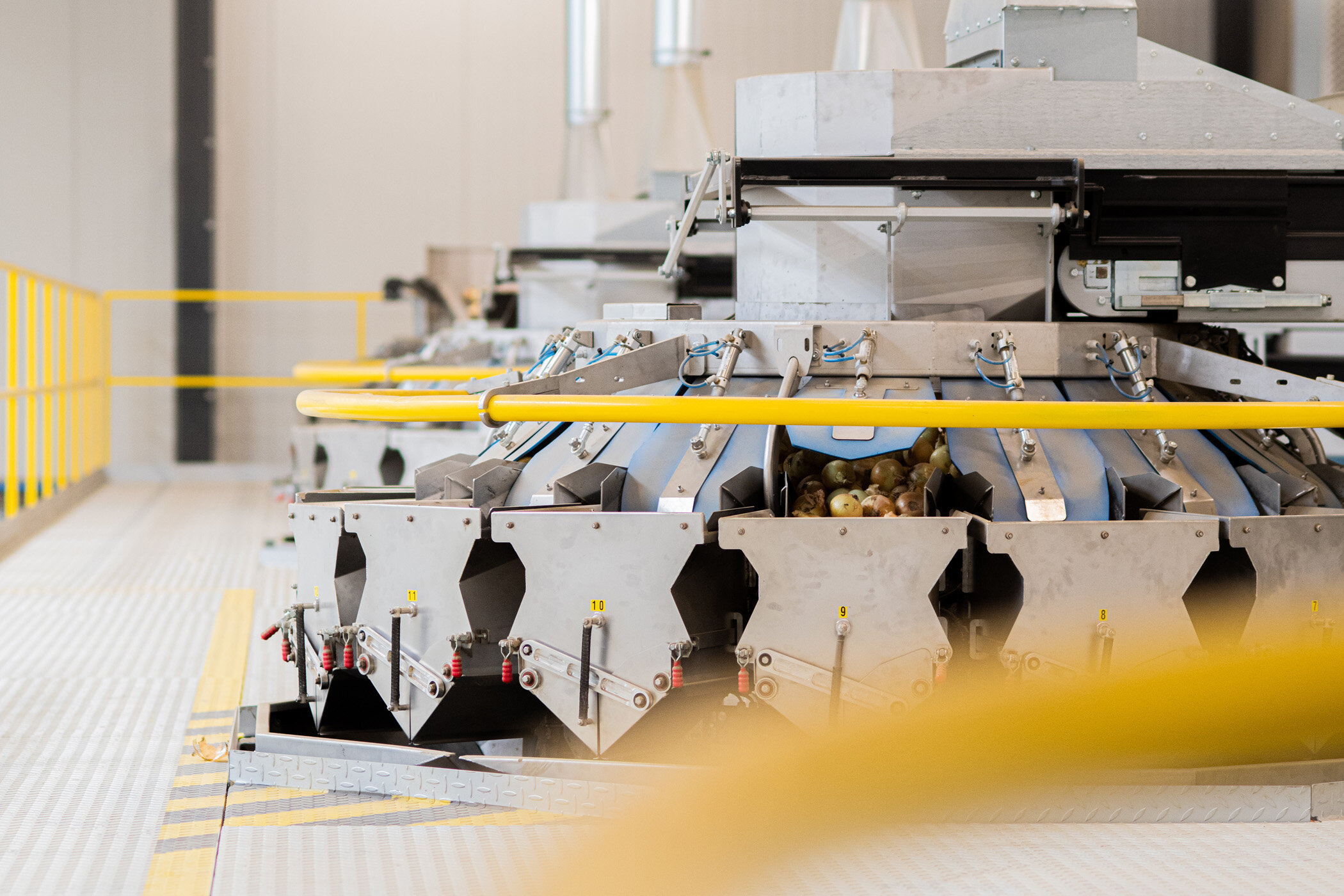
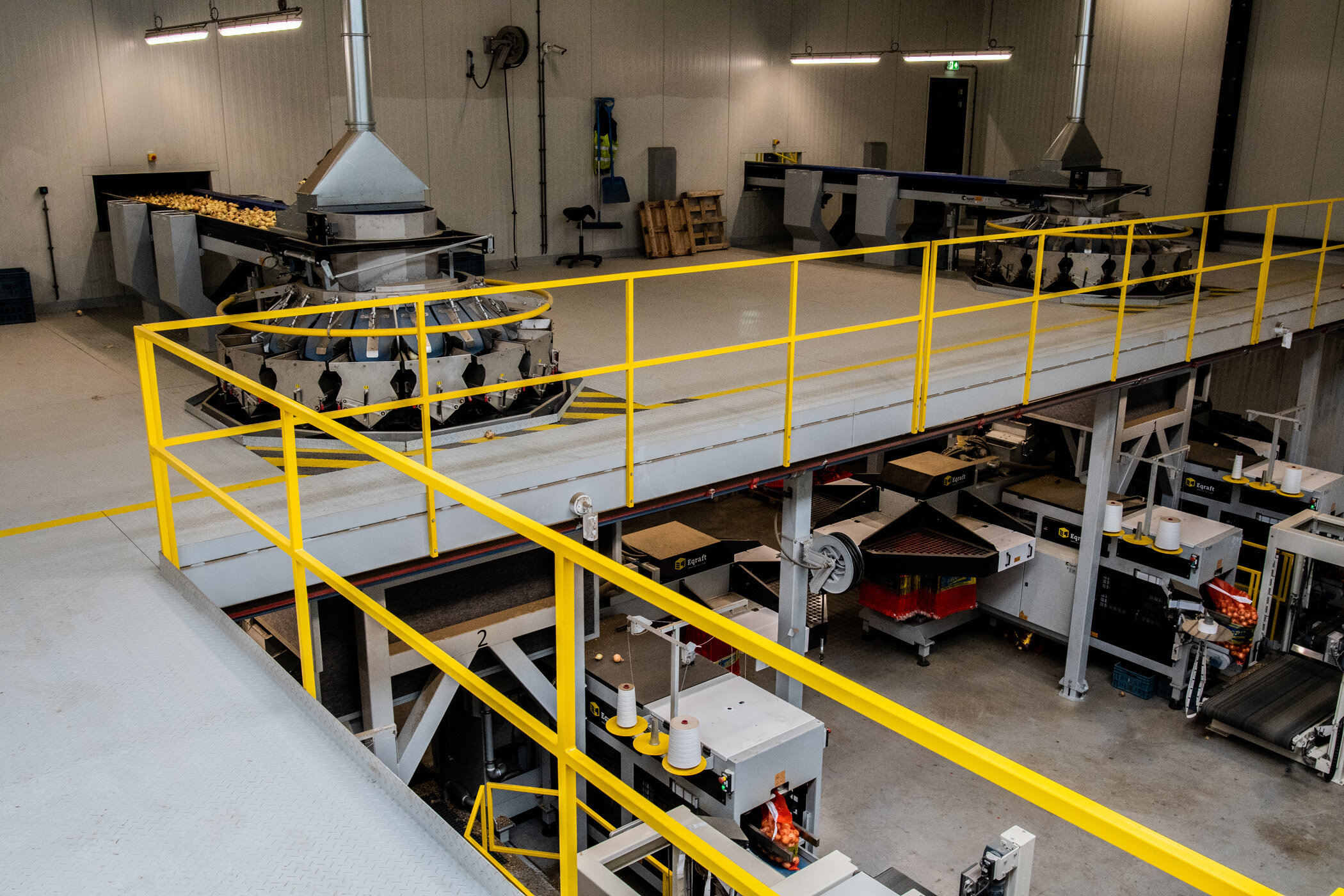
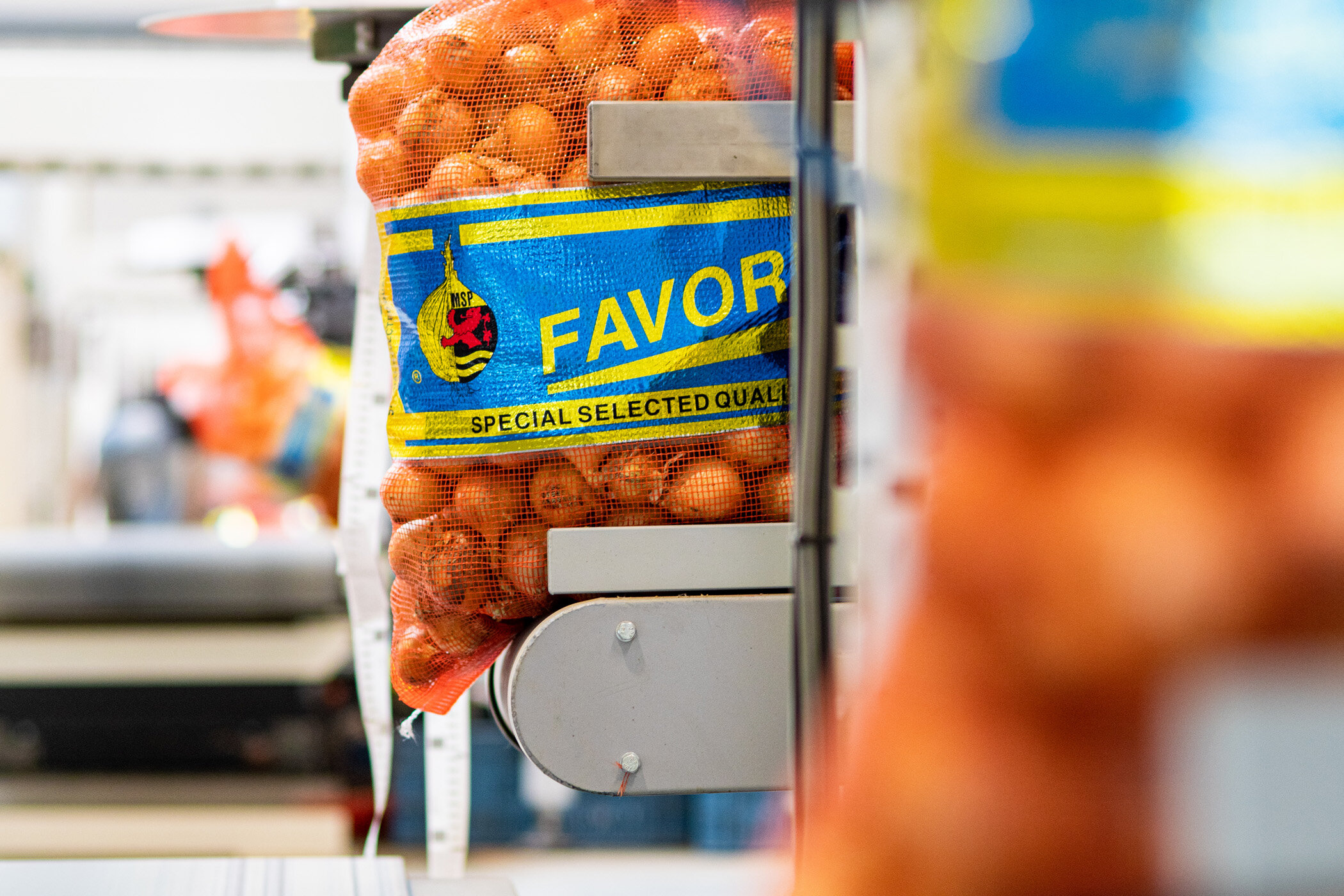
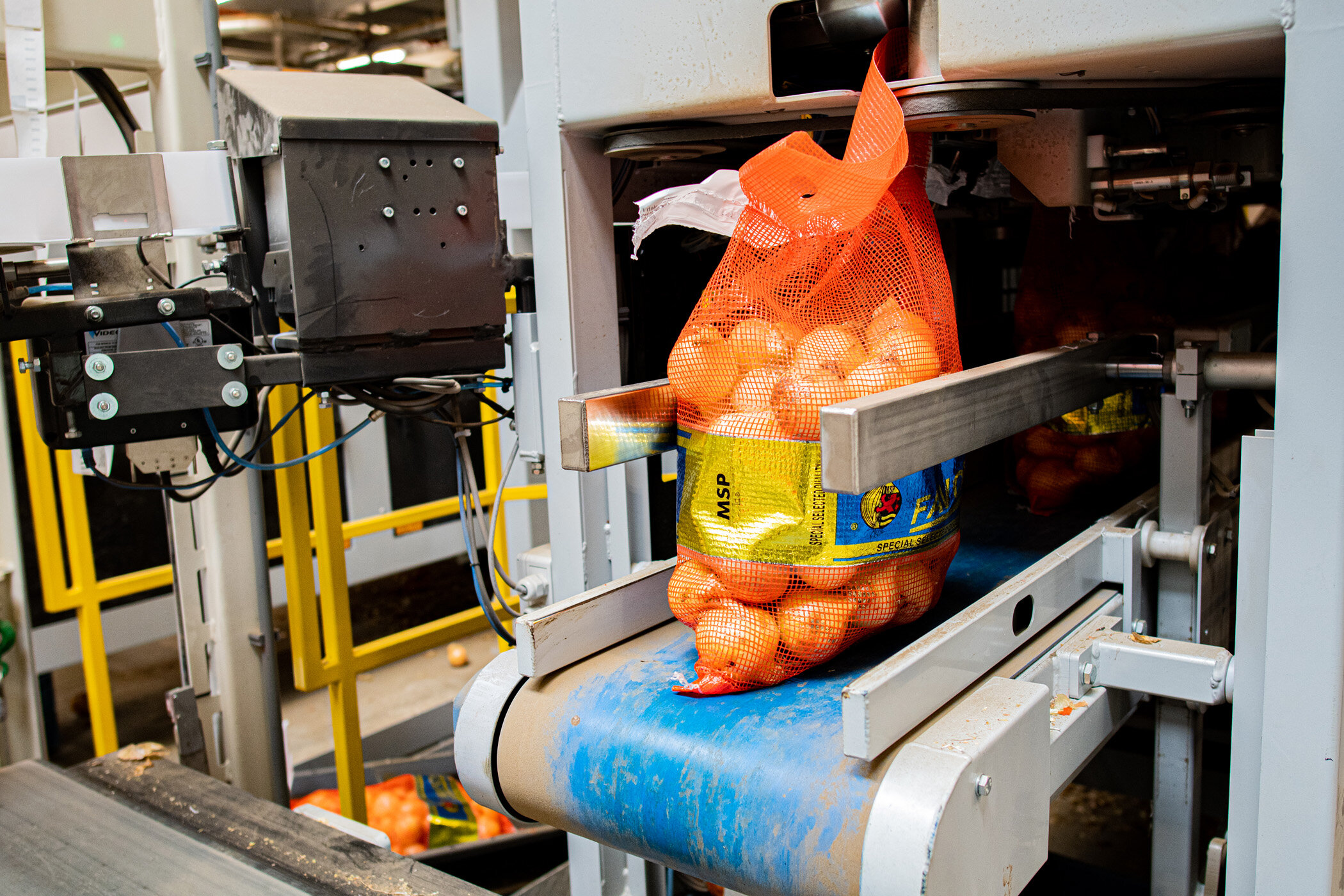
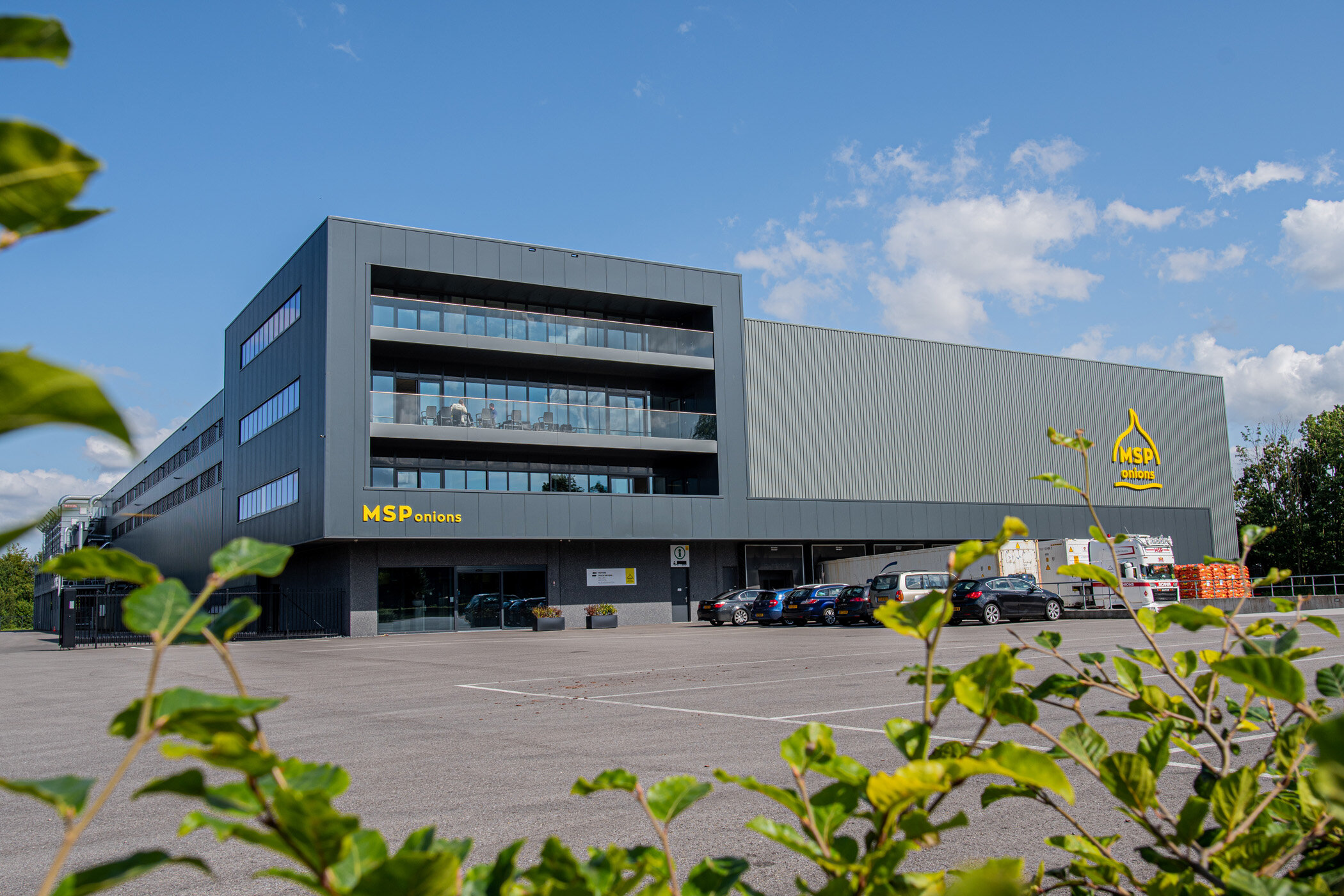
100 percent quality
Since the onion processing line was launched in September last year, MSP Onions has been discovering all the possibilities on a daily basis. In April, we had got so far that customers were able to say which type of onion they wanted and we could guarantee 100 percent quality with not a single wrong onion in the batch. That was the biggest benefit, a guarantee on exports. It allowed us to grow counter-cyclically in the low season while the entire sector was slowing down,’ says Lindert Moerdijk, sales director at MSP Onions. Another important advantage is the deployment of personnel. ‘Traditionally I would have needed around seventy people but now I can double the capacity of the sorter with one man. As you can imagine, that has huge commercial benefits.'
“We could guarantee 100 percent quality with not a single wrong onion in the batch.”
Turbulent history
The showcase has a turbulent history. Just as construction was due to start, Eqraft went bankrupt due to a combination of circumstances: organizational change, new people, a major project, differences of opinion, adversity in the market and financial setbacks. ‘Because of the shared interest, we then set up a temporary project company and MSP helped us with the cash flow so that we could finish the factory,’ explains Keurhorst. Eqraft also collaborated on the project with Symach (layout and palletizing systems), Modesta (air treatment, dust extraction, waste management) and Deprez (internal logistics). ‘We’re active all over the world with these parties. Engineers, people on the shop floor, implementation and assembly all know each other so you can always go one step further.' MSP also entrusted the overarching software and control to Eqraft. A link between the factory control and ERP system, implemented by Eqontrol, makes the factory so smart that when orders arrive the factory knows exactly which onions are in stock and sets up an intelligent production schedule on that basis. ‘Thanks to the enormous drive from all involved, we finished the project on time and we can now show the world what’s possible.’ Moerdijk endorses this: ‘In the end, with the capabilities of both companies we succeeded in bringing this project to a successful conclusion. And now we’re running successfully with the new factory.’ The Sales Director of MSP Onions still has lots of plans. ‘I can see thousands of opportunities for new projects, but it’s still a bit too early to be specific. We first need to bring this business plan to fruition. This sorting technique isn’t yet widely used in the sector so it means there are lots of opportunities for us.’
A more strategic approach
Eqraft is now back in business under new management. Engineering, software development, project management, purchasing, production and service are concentrated in Emmeloord, with the day-to-day management in the hands of General Manager Marcel Kampes. And in Goes, Keurhorst and his team focus on consultancy, project engineering, sales and marketing. In just two years, the company regained the confidence of the market, expanded the workforce from eighteen to fifty, carried out around fifty projects and is making a profit again. ‘We’re working more efficiently now, which means we’re also operating with a margin. Added to that, we’re growing all the time and our order and quotation portfolio is well filled. As an organization, we try to look strategically further ahead and we’re already busy with projects for 2025. Because you never know what’s going to happen and not one business plan predicted the pandemic. And our competitors are busy too. That world is so dynamic that you always need to be focused in order to stay on course.'